Mattel
Industry
Location
THINKERGY PROCESS INNOVATION CASE
Information
Thinkergy was approached by Mattel in Bangkok to work with its managers to improve their problematic process planning for its toy car production in Thailand. In briefing discussions, we quickly noticed the root of the firm’s problems: Huge complexity caused by the number of different production designs, as they had to plan 5 new ones into production each day. This would lead to over 1,250 different production designs, over the course of the year.
In order to fix the critical bugs in the production planning process, Mattel and Thinkergy agreed to “work overtime” in a rapidly organized 3-day X-IDEA Innovation Project. We worked with three multi-functional teams coming from Mattel’s relevant business units to develop ideas for redesigning the critical front-end production planning process, aiming to help the firm save costs and time (critical factors in the fast-moving and highly competitive toy industry).
Among many other X-IDEA Tools applied in the project, one proved to be invaluable: We asked the participants to map out the “Customer Journey” of a model toy car, travelling through the various stages of the planning and production process. We distinguished the process steps, documents and databases involved, and highlighted critical problem areas and bottlenecks. After creating the Customer Journey Map to gain insights into key issues, participants generated raw improvement ideas, which were then developed into meaningful “bug-fix” Idea Concepts.
After implementation of the top Idea Concepts delivered by the X-IDEA Innovation Project, Mattel’s rejection rate soon dropped significantly and the production planning process saw a speed increase; leading to considerable cost savings for the company.
Client
Category
Share
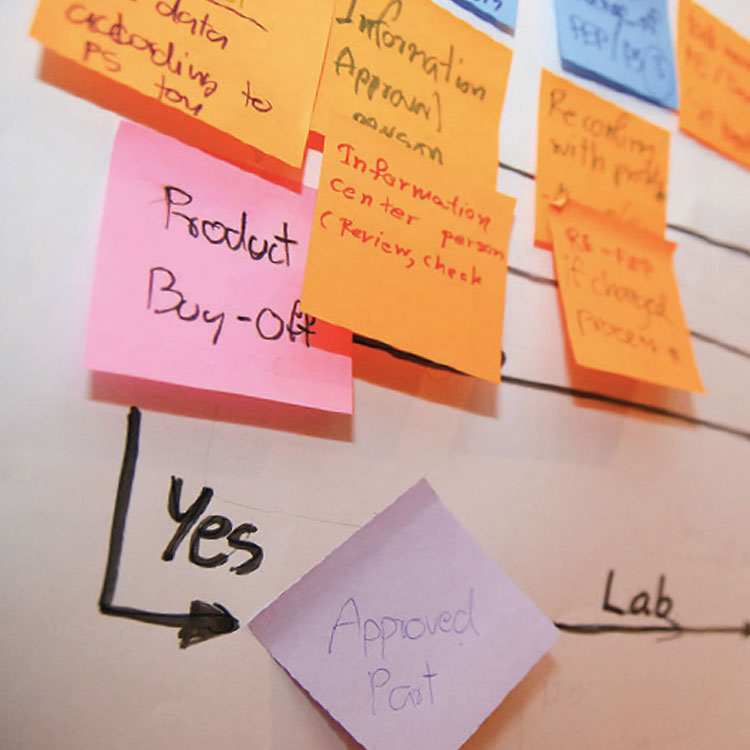
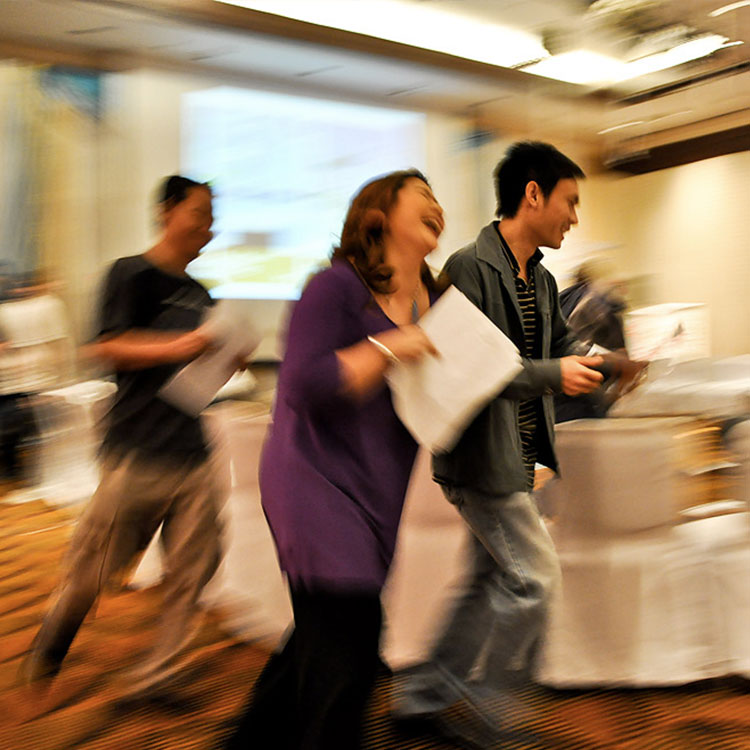